Ion exchange and adsorption
in a few words
Ion exchange (IEX) is a mechanism that removes ions or other compounds, often considered as impurities, from a liquid solution by exchanging them with ions of similar charge on a resin through a reversible interchange. This basic principle involves the use of an ion exchange resin, which is a polymer matrix containing functional groups capable of linking and exchanging ions.
Adsorption is a mechanism for separating molecules from a liquid mixture using the capacity of a porous resin to link reversibly with certain molecules in particular.
Given the similarities of these two mechanisms, often happening together, at Applexion, we call purification processes using these two mechanisms under Ion exchange technology. This technology is commonly used in numbers of industries such as water treatment, electronics, mining & metal refining, chemical, pharmaceuticals and of course Food, Functional ingredients, Fermentation, Biotech and Biobased molecules.
Ion exchange
Industrial technology
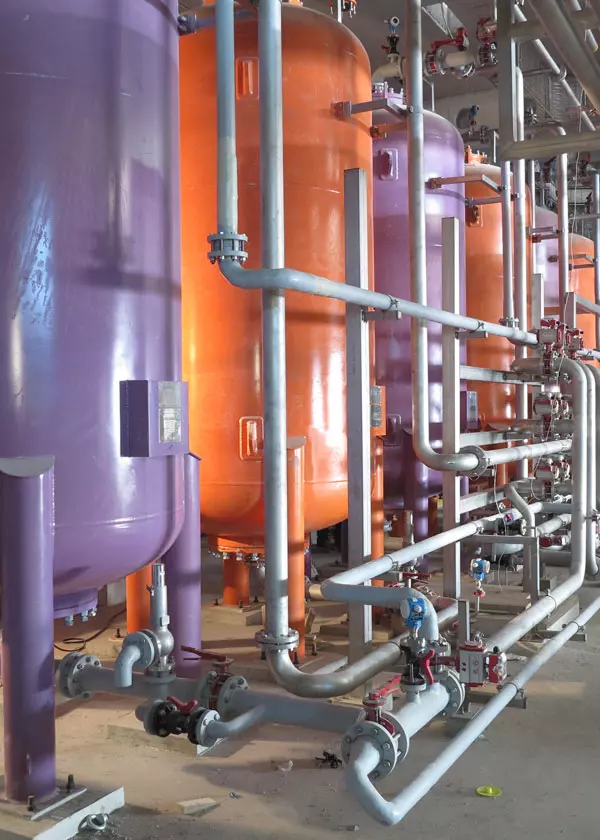
Ion exchange is used for numbers of applications, to remove specific components for a liquid (macromolecules, color, all or some specific salts).
For doing so, it uses low temperature, low energy, solvent free properties of the different components in a product, that will interact with the ion exchange resin, such as ionic charge, H-bonds or hydrophobicity.
The efficiency, the robustness and the quality obtained by using Ion exchange are key to its popularity. Here are some key advantages of Ion exchange technology:
Can be applied to various industries and processes, including water treatment, wastewater treatment, pharmaceuticals, food and beverage, and chemical manufacturing. The flexibility of ion exchange resins and their ability to target different ions contribute to this versatility.
Feasibility: Validate purification levels and technical feasibility.
Scale-up: Validate industrial performances and optimize process.
Small production: Produce samples for market testing or full production of small quantities.
Capability of producing high purity by removing impurities in principal streams but also for effluent treatments.
Resins can be regenerated hundreds of time, extending their lifecycle and participate to make the process cost-effective.
Can be scaled up for industrial applications, making them suitable for both small-scale and large-scale operations.
Multiple hundreds of highly specialized systems and thousands of m3 of specific consumables (resin) currently in use.
Ion exchange process
Resins, the fuel of the industrial
ion exchange process
The fuel of the ion exchange process is the resin. Operating conditions and the properties of the resin influence the separation and are critical parameters to be studied in details.
These resins are typically made of organic polymers with special functional groups attached to their structure. The functional groups determine the type of ions the resin can exchange. The functional groups on the resins are charged, either positively (cation exchange resin) or negatively (anion exchange resin). Resins are classified onto different categories :
- Strong acid cationic resins.
- Weak acid cationic resins.
- Strong base anionic resins.
- Weak base anionic resins.
- Polymeric adsorption media and activated carbon.
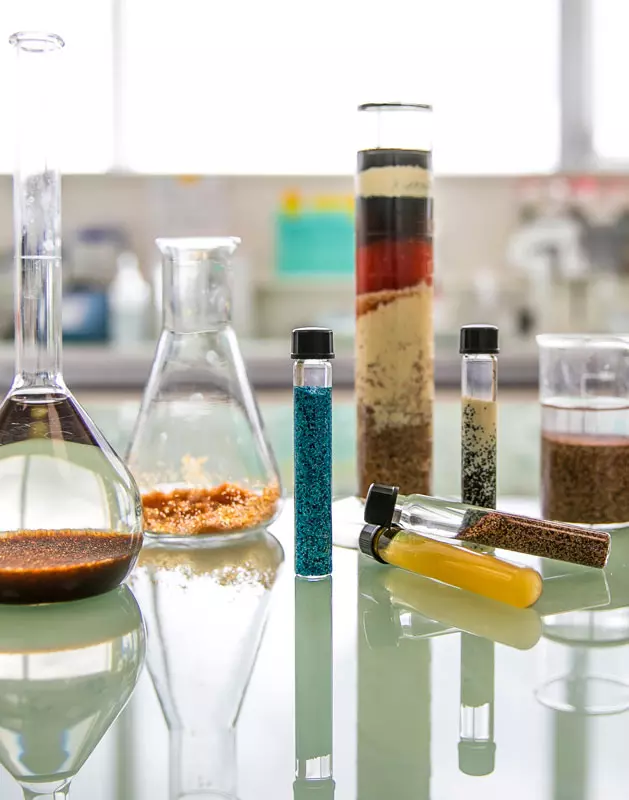
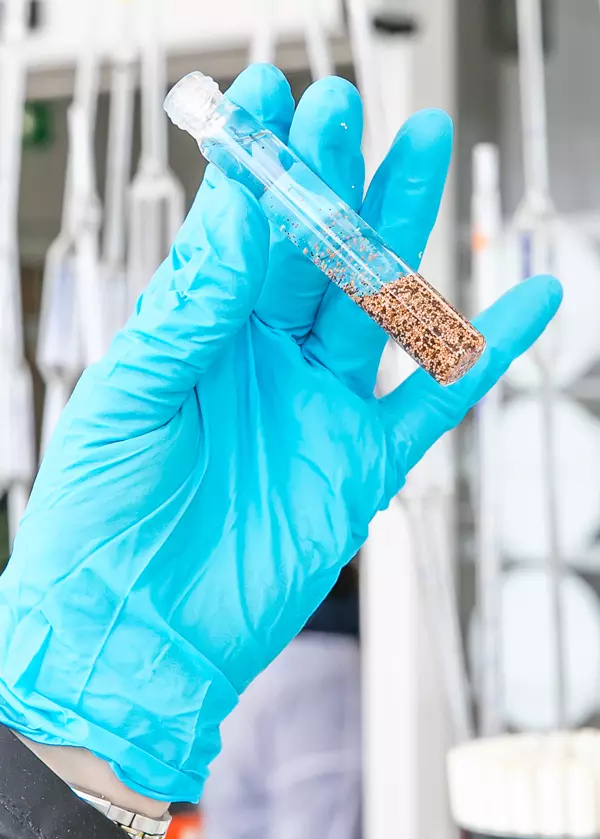
While in contact with the product under given operating conditions, the reversible exchange between the product and the resin reaches its equilibrium: the resin becomes “saturated” with exchanged ions, and its separation capacity stops. To restore the resin capacity, we shall first reverse the interchange by changing operating conditions: This “regeneration” step involves generally passing a concentrated solution of the initial exchanged ions through the resin bed, releasing the captured ions and restoring the resin to its original form.
Our expertise in designing ion exchange and adsorption processes, combined with laboratory and pilot plant evaluation, allows us to provide best-in-class resins and set of operating conditions specifically adapted to your application.
Each Applexion™ XA resin is selected according to a strict benchmark and extensive analysis of its behavior under industrial conditions. We also make sure that each Applexion™ XA resin compatible with intensive industrial activities. Learn more about our resins.
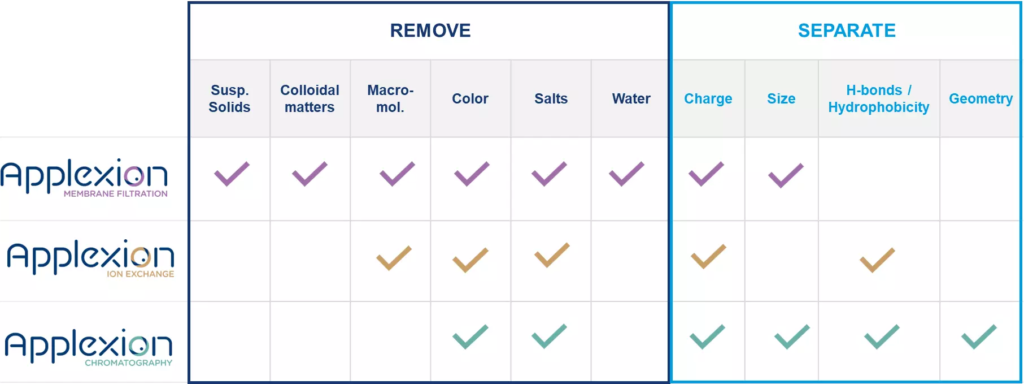
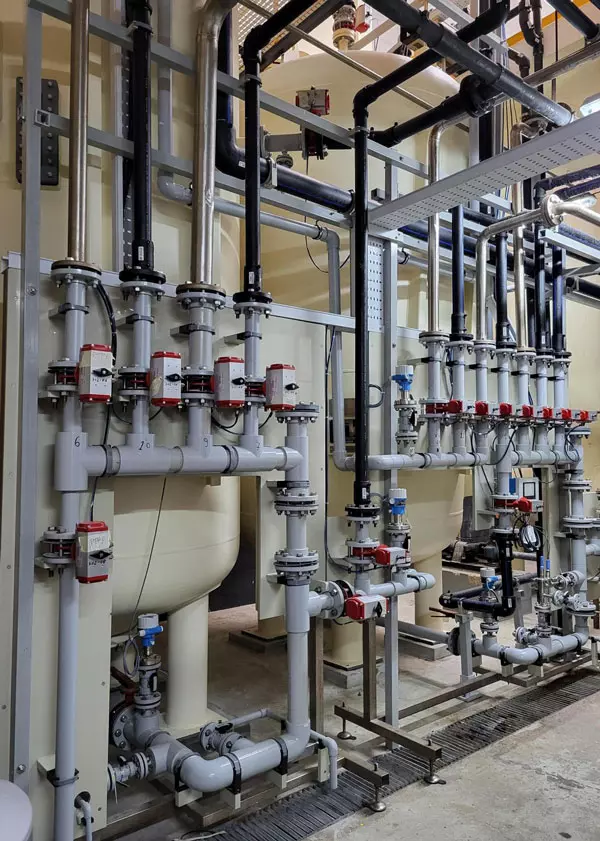
The System,
the engine of the industrial ion exchange process
Applexion™ IEX, robustness and versatility for industrial systems
At Applexion, for more than 50 years, we develop, design, fabricate and serve ion exchange systems in special applications. Mostly in course Food, Functional ingredients, Fermentation, Biotech and Biobased molecules. We are using our expertise to develop custom made system designs for a given application and to adapt to numbers of industry standards.
From R&D to plant start-up and beyond, Applexion™ offers a one-stop shop for all your purification projects: optimization of well-established applications as well as development of efficient purification processes for new products.
Key criteria expected of on industrial system are:
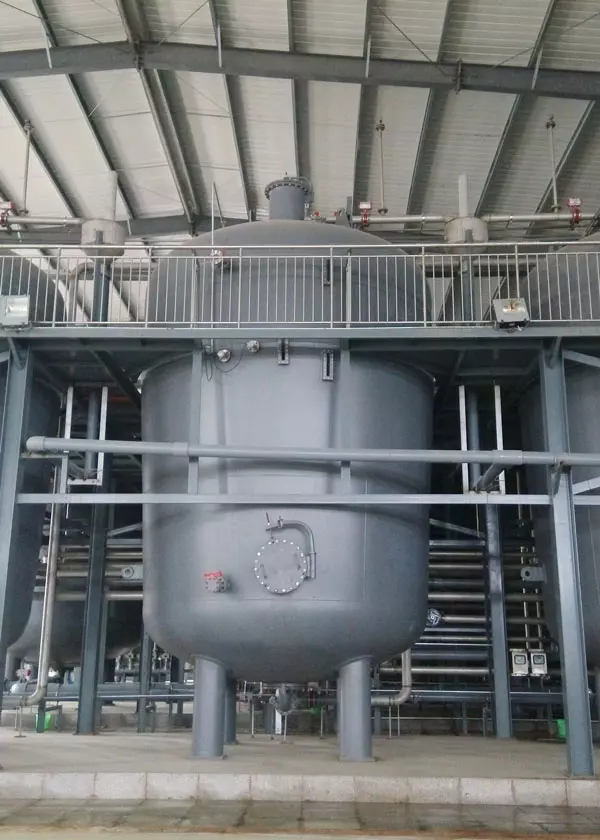
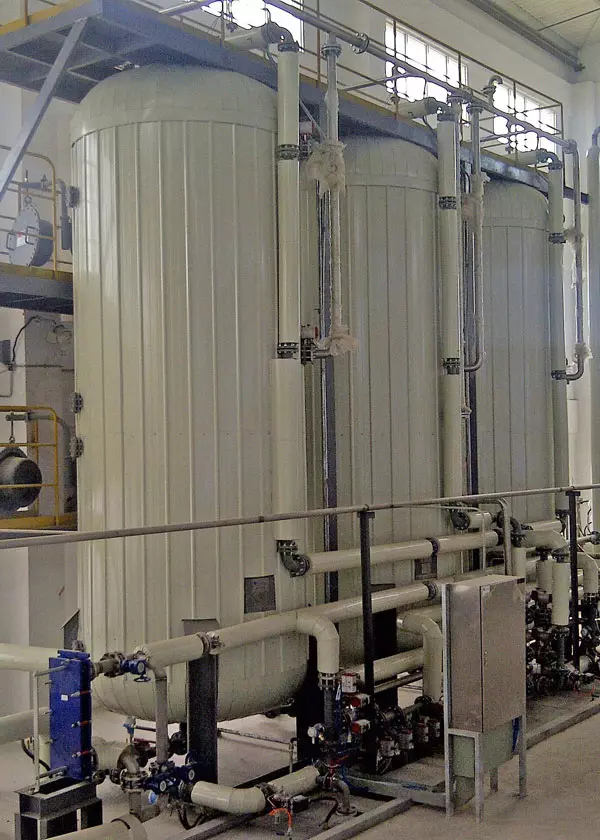
Applexion™
continuous ion exchange
Applexion™ continuous ion exchange offers the industry the benefits of a truly continuous ion exchange system. In a continuous ion exchange system, the flow of the liquid through the ion exchange resin bed is constant, allowing for a continuous and steady-state operation.
In specific cases, this approach offers several advantages over batch processes, such as increased efficiency, consistent product quality, and reduced downtime.
Depending on the process, the number of cells can be adapted to optimize resin utilization and minimize system size while balancing overall capital investment and operating costs.
Key features of the Applexion™ continuous ion exchange system are:
A continuous flow of feed, water and effluents, easier to control and monitor.
Allows for the treatment of larger volumes of solution, making it suitable for industrial-scale applications.
Enables better control over the exchange kinetics and maximizes the utilization of the ion exchange resin.
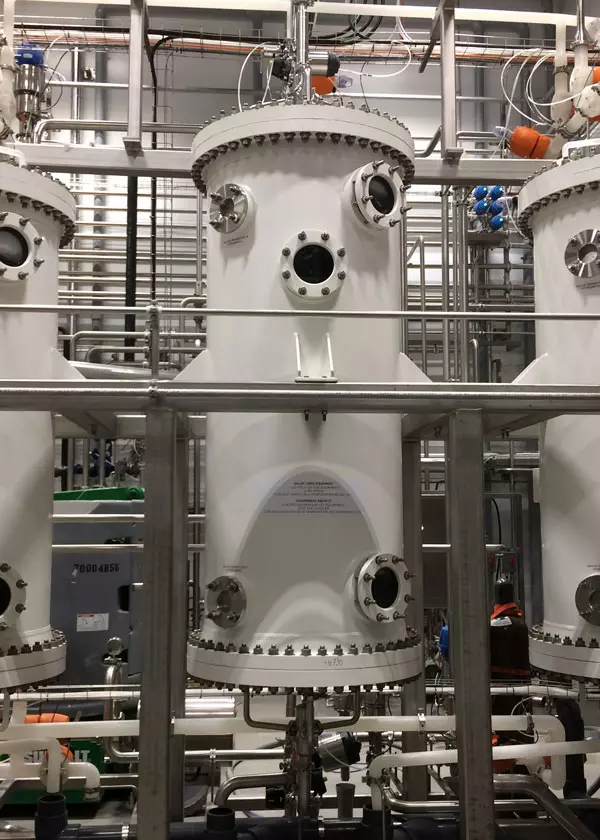
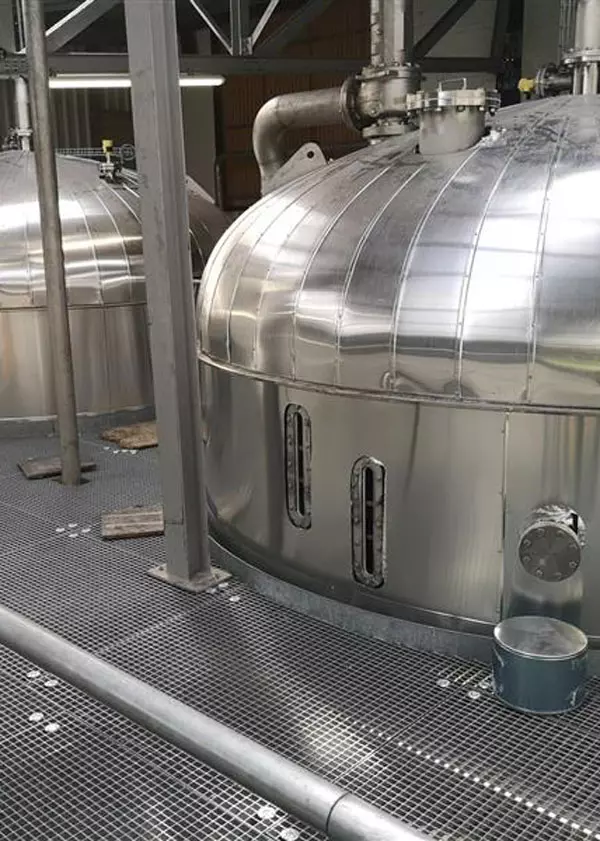
Applexion™ NRS
The reference for juice softening in sugar factories
- The juice is softer, reducing the need for anti-scaling agents
- Evaporators require less cleaning and are significantly more efficient
- The final sugar quality is improved thanks to reduced turbidity
- No dilution of the juice and no additional acid/water are required
- Zero effluent and waste generated thanks to a smart recycling design
Ion exchange
Let’s get more technical
By following our step by step methodology, we minimize scale up risks,
we shorten time to market and we maximize performance and cost efficiency.
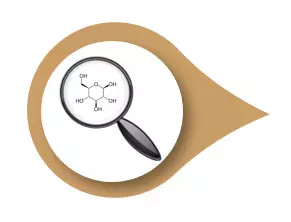
The very first point to start is the definition of the raw material to be purified. Which allow to define the final quality of the product and impurities to be removed. The quantity and the nature of these impurities will determine eventual pretreatments and the strategy of purification.
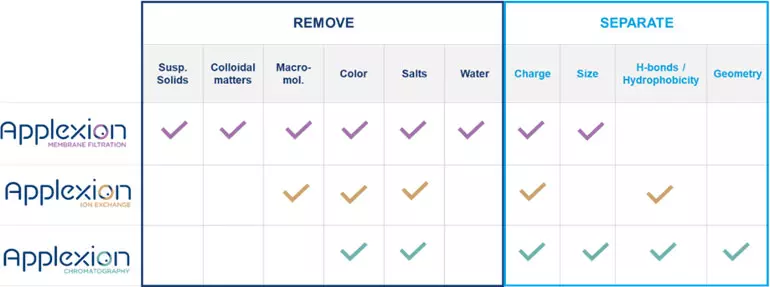
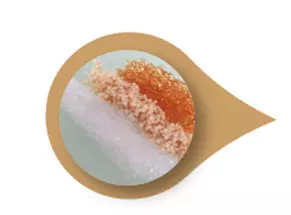
A screening of the IEX resins is perform at lab scale. Pre-selected resins are tested and compared regarding the performance of the separation and regeneration. Resins are selected from our XA library, benefiting from our +50 years experience on industrial systems. Availability, regulatory aspects, quality, resistance to various stresses of the resins when going into industrial scale are key criteria of the selection.
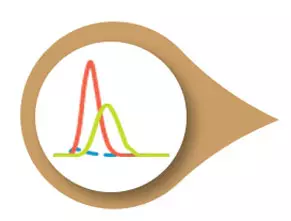
One of the unique expertise of Applexion for a process development is digital modeling and process simulation. By combining experimental results of the current project, previous experience and our unique in-house software, we considerably increase the reliability of our results and hence the confidence in estimations that we can deliver at early stage of process development.
Numerical approach requires less raw material, smaller size of equipment and less time to explore a wider range of solutions. Moreover, it gives the capacity to test different constraints and to investigate in details the robustness of the design of the process. It is key for all new applications, where decades of feedbacks and learning are not available.
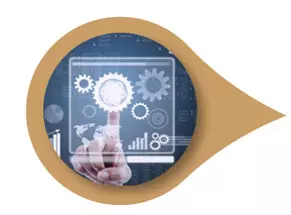
Here we build a design based on process simulation. A first mass balance is established with key values : size and design arrangement, flow rates and an estimation of the composition of the products obtained. It includes all consumptions such as process water, electricity, streams and related costs. This work, done together with by the process engineer and supported by technology experts, will give a first evaluation of the CAPEX and OPEX of the system, benefiting from all Applexion experience in up-scaling from lab scale directly to industrial large system.
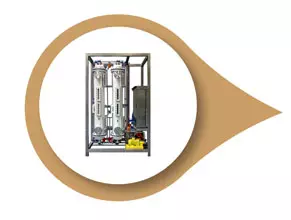
After this process evaluation based on lab screening and process simulation comes the next step for robust scale-up. Through pilot tests, key process settings corresponding to suitable performances can be confirmed or adjusted. Data for sizing can be confirmed and the robustness of the industrial process design proven. Piloting is not only process-oriented, but can be also product-oriented: the customer may need some kgs of product for market tests or further downstream trials.
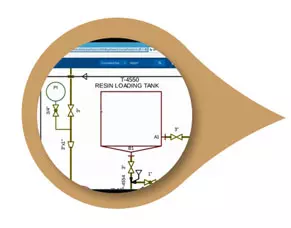
The precise process design given with process performance guaranteed is the natural outcome of all the previous steps. At each step, an open dialogue with our customers allow a design customized to your specific needs and Applexion quality.
Ion exchange
Applications
Typical applications of the IEX technology include the production of:
- Demineralization and softening.
- Salt conversion.
- Decolorization.
- De-acidification.
- Adsorption.
Frequently Asked Questions
What are the typical regenerant used in Ion Exchange?
There are variety of regenerant that are used, and the selection of a regenerant will depend on the type of resin and the reversible exchange you need to make.
The most common regenerant are: HCl: Typically used on cation resin, where you want to place back H+ groups on the resin and push out cationic minerals (Na+, K+, Ca++, …). The use of this acid requires a special attention to corrosion on the system and it’s environment.
NaOH: Typically used on anion resin, where you want to place back OH- groups on the resin and push out anion minerals (Cl-, SO4–, …). Mixing of regenerant streams from Cation and Anion often creates a salty wast stream mainly composed of NaCl and the minerals that have been pushed out from the resin.
NaCl: Typically used for asdorption regeneration, for exemple in decolorisation application. Often, NaCl brine can be recovered and reused for next regeneration through our several Brine Recovery Systems.
Numbers of other acid, base and regenerants are also often use, such as H2SO4, NH3, EthOH, …. Selection of the right regenerant and recovery possibilities are becoming a key design parameter that we discuss with customers in R&D and design phase. It has consequences in environment integration, OPEX, product quality, water / utilities consumption and Carbon footprint from operation.
What are the advantages of Ion Exchange ?
How often do I need to replace my Ion Exchange resin ?
It depends.
There is really no generic rule and it depends of plenty of factors affecting the resin properties. Among main factors, they are the ones affecting the structure of the resin beads, and therefore the hydromechanical limits of the resin + system, and the ones affecting the functional groups of the resin, either reversibly or irreversibly. From these basic principles, specific “guidance” per application are commonly used, but are far from optimized. In real life, it is often difficult to find a clear “trigger” decision, and following this guidance, combined with maintenance schedule is a widespread practice. At Applexion, we are supporting initiatives to increase the lifetime of the resin at its maximal , in order to lower replacement costs and to reduce carbon footprint down to lowest possible level.
It starts with selecting the resin taking into account lifetime resistance. It also includes proper & regular monitoring of resin use during operation, adequate resin properties preservation through proper risk management and adequate resin regeneration procedures at the right time.
Why choosing Applexion ?
and offering on Chromatography, Ion exchange and Membrane filtration technologies.
The only global player, all over the world and all over the life cycle of your equipment.
You have a new one to share?