Design & Build
Let’s design & build together
the best purification process
to your needs.
- Save up to 50% in R&D.
- Save up to 50% in start-up.
- Save up to 50% in production costs.
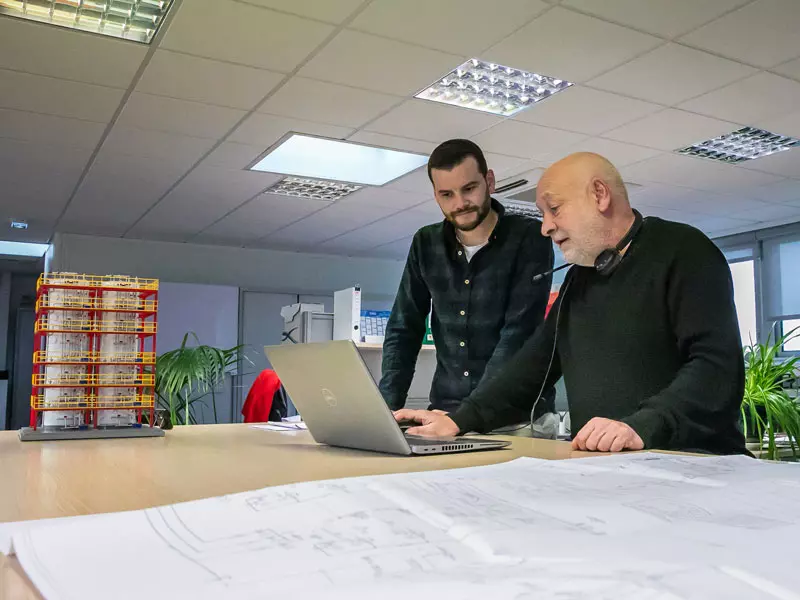
This is for You, if You’re
And you want to save up to 50% of time and derisk your lab & pilot scale R&D development.
- Unique resin & membrane screening & testing plateform.
- State of the art modelisation capabilities in chromatography, ion exchange and membrane filtration.
- Pilot testing at our places or at yours, with remote digital services.
And you want to design and build at your standard and Applexion quality. Save 50% of time and resources on installation & start-up.
• Adapt engineering & documentation at your standard or keep Applexion one thanks to our advanced engineering platform.
• Fabrication following industry and local specifics (ASME, CE, Sanitary, …).
• Adapt choice of electromechanical equipment to your plant standards.
• Latest programming platform ISA88 compatible for easy plugging in existing automation system, fast testing and intuitive operation.
• Water, utilities and time saving up to 50% in testing and start-up phases.
And you want to save up to 50% of cost and greenhouse emissions by boosting the purification performances of your systems.
- Full carbon footprint of your project, scope 1, 2 and 3.
- Benchmark solutions with sustainability and economics criteria.
- Add our performance boosters to your processes. Save from 30 to 100% on water & utilities usage.
- Unique set of Industry 4.0 services for optimal production every day.
Tell us about your challenges
whether it’s extracting a specific ingredient from a feed,
validating a purification process before scaling up,
conducting pilot tests to verify your process’s feasibility,
or leveraging our engineering competencies to design your process.
From lab to industrial
Your project is designed and built
at your standard and Applexion quality
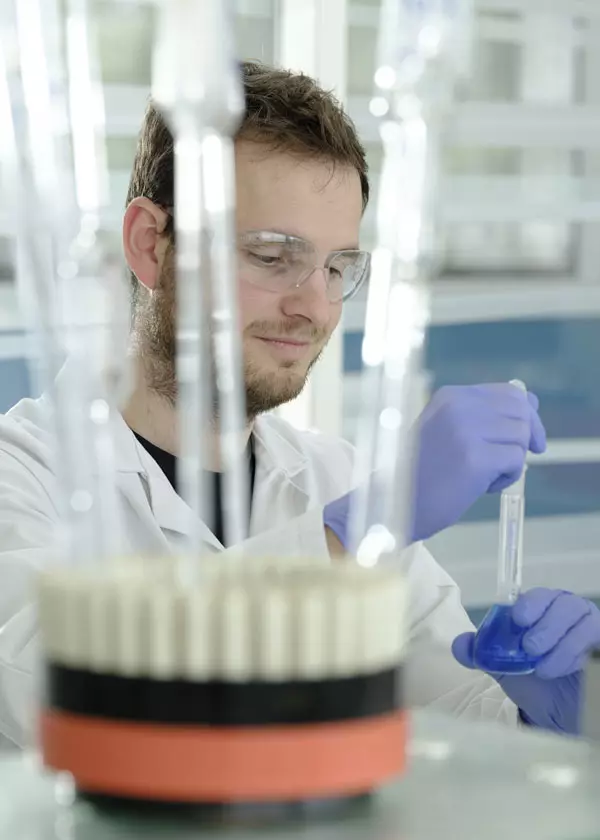
From feasibility
to process
Our R&D team, passionate group of technicians, engineers and PhDs, work on 30 to 40 processes each year.
They measure and characterize the critical parameters of your process and consumable use through our multi-steps methodology. On a need basis, we can transfer analytical methods or develop new ones.
- Proof of Concept = Does it work?
- Identification of Key Process Parameters (KPP).
- Lab: study of KPP.
- Estimation of process settings and performances.
- Data acquisition for preliminary CAPEX/OPEX.
- Bench / Piloting: validation of process settings & performances, representative streams (final product, side streams for recycling or build-up estimation & experiments), refined estimation of CAPEX/OPEX.
From workable
to optimized design
One of the added values of Applexion for a process development is modeling and simulation.
By combining experimental results, experience and unique in-house modeling software, we significantly increase the reliability of our results and thus the confidence in the estimates we provide.
This numerical approach requires less raw material, smaller scale equipment and less time to explore a wider range of solutions. It also provides the ability to test different constraints and analyze the robustness of the design. Because a design study is not complete without cost associated with it in terms of CAPEX and OPEX, as industry scale specialist, we provide a wider range of economic scenarios.
Feasibility: Validate purification levels and technical feasibility.
Scale-up: Validate industrial performances and optimize process.
Small production: Produce samples for market testing or full production of small quantities.
All pilot units can be customized to meet specific needs.
- First load of consumables (resins/membranes) included.
- Additional consumables available upon request.
- Training, remote or on-site support available upon request.
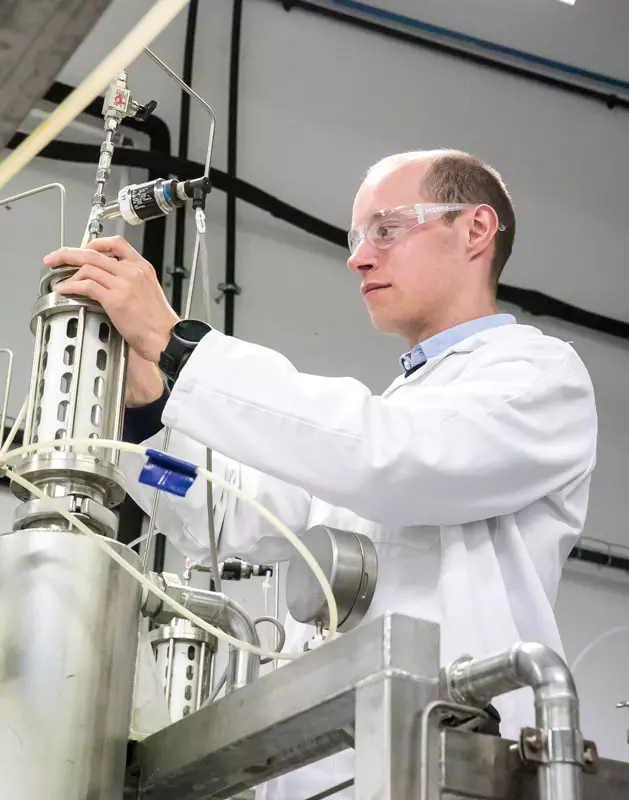
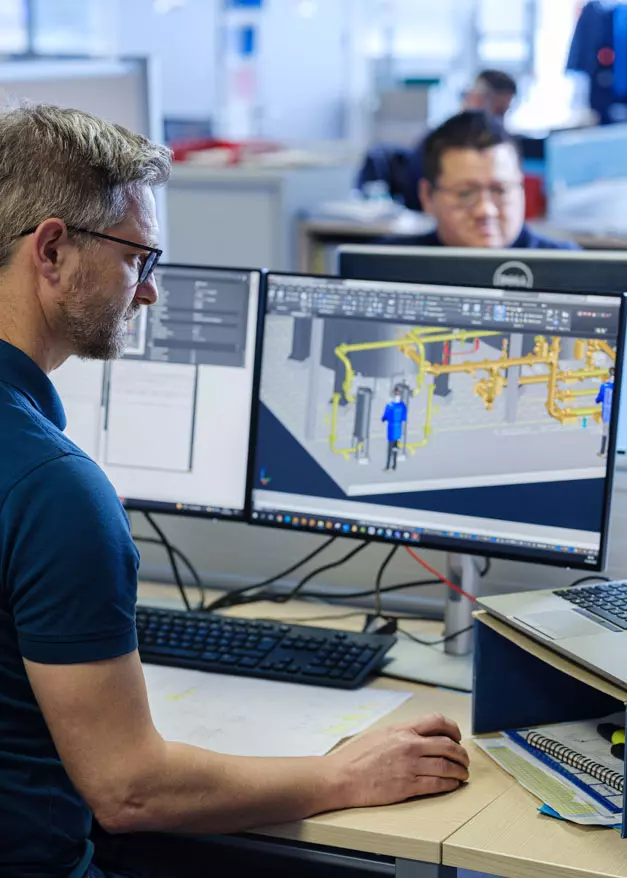
From basic
to detailed engineering
Hand-in-hand with the R&D teams, our process experts design and size your process to be compatible with industrial operating conditions. Our industrial technology experts make sure you are provided with the most cost-effective solutions to deliver your product at specifications.
Our engineering team generates PID and 3D views of the final design of each unit operation. Electricity and automation designs are finalized while the specifications of each material component are defined.
From the beginning a project management team is dedicated to your project that includes our purchasing department, supply chain experts, quality department and experienced project managers.
The purchasing team deployed in Europe and Asia works with First in class manufacturers while the QC team checks on the quality of any custom fabrication. The system routing, as a whole or in sections, is managed by our supply chain experts up to the client’s factory site and the assembly is followed locally.
- We work with a network of reliable suppliers for manufactured equipment sourcing.
- Custom vessels and skids fabrication on 3 continents.
- Competitive sourcing with large platform in Shanghai.
- Quality control by Applexion with dedicated QC team.
Installation
and commissioning
Our commissioning engineers, together with process experts, come on-site to fine-tune the process parameters and to perform all necessary tests before start-up. The unit is started up by Applexion and your Production & Maintenance team are trained to operate the system safely and with the best operating practices.
- Standard automation remote access.
- Commissioning with local partners and remote expert assistance (successfully in place in Indonesia, Brazil, Germany, Balkans, US).
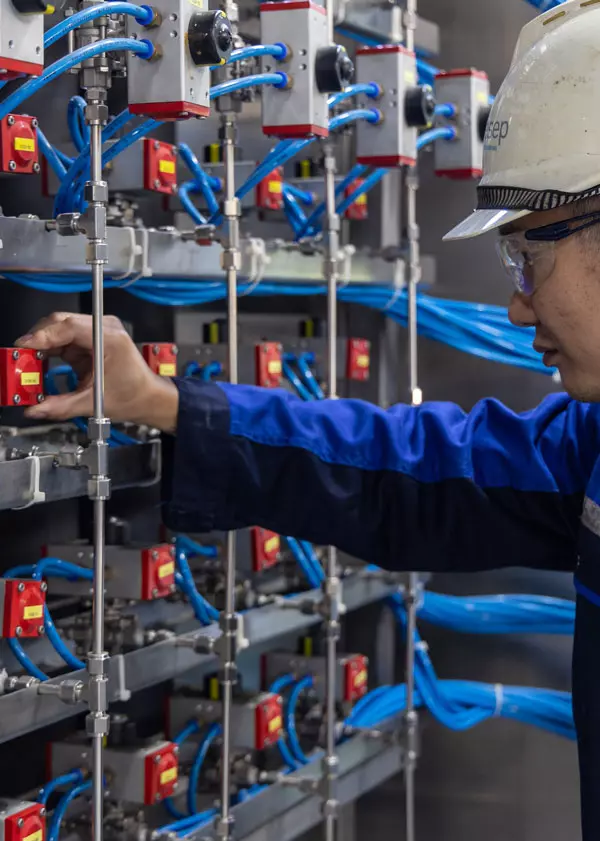
Design & Build
Our resources
Why choosing Applexion ?
It is on these strong roots that Applexion has decided to strengthen unique expertise
and offering on chromatography, ion exchange and membrane filtration technologies.
The only global player, all over the world and all over the life cycle of your equipment.
You have a new one to share?
Frequently Asked Questions
Does Applexion need a lot of product to make process development on a given application?
No, as start, we would require less than a liter of product. Thanks to our consumable screening platform, our characterization methodology and in-house softwares, we can do most of the R&D work and explore a large range of consumables and operating conditions with very little amount of product and time.
Does all the R&D work need to take place at Applexion R&D centers?
No, our methodology is designed so that parts of the experiment can also be made at your place. From lab to pilot stage. Thanks to remote digital services, you will be able to pilot in optimal conditions. However, our R&D facilities are designed, and our R&D teams trained to cope with the high specifics of doing research with Applexion technologies. It is a guarantee of quality, exhaustivity and rapidity in R&D development.
Can Applexion meet the engineering standard of my industry?
Yes, for a very large set of industries using our technologies, we are regularly designing and manufacturing systems adapted to the industry or regional specifics. From Chemical to Dairy food standard, From Food & Beverage to Biotech standards. Pressure vessels codes & stamps, weldings and connectors, electrical norms, electromechanical brands and standards, … But also customized engineering documentation and codification, easy program integration.
Are Applexion systems easy to install / skid mounted?
Is carbon footprint a criteria that Applexion takes into account when designing a process solution?
Yes, we are deploying an carbon footprint calculation for all our system offers. It includes scope 1, 2 and 3. And we are priding ourselves to suggest performance boosters as much as we can, benchmarking solutions with sustainability and economics criteria. They often save from 30 to 100% on water and utilities usage!
What is your plan of reduction of carbon emissions?
Although our findings show that most of the carbon emissions to be saved is by the optimization of the operation of the system and of its integration in the overall process, we also work in minimizing our scope 1 &2 through numbers of initiatives. Our unique set of design, performance boosters and Industry 4.0 services target is to tackle +800,000 tons of CO2 eq emission per year through optimizing existing manufacturing assets.